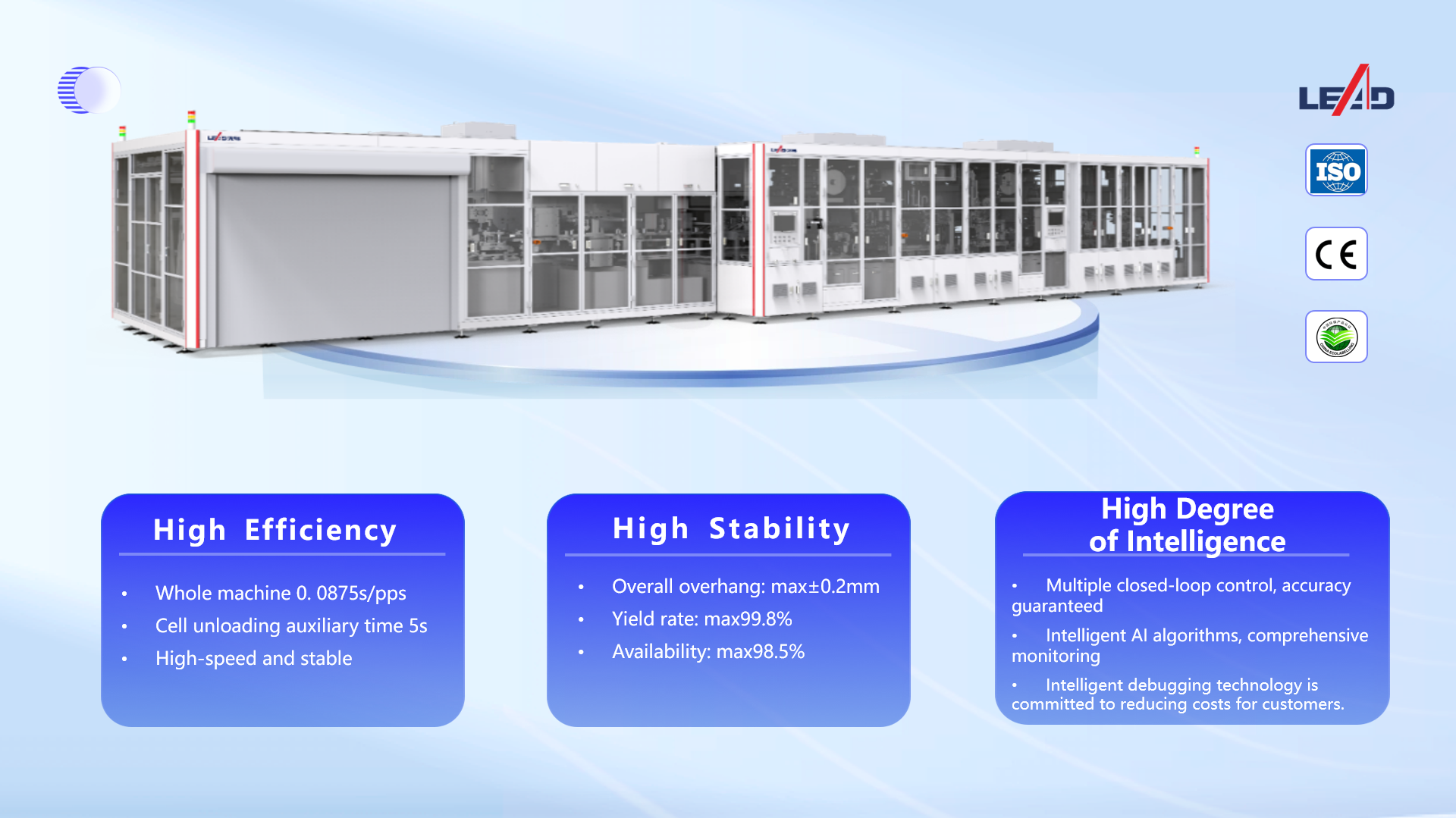
An all-solid-state battery (ASSB) is an energy storage device that replaces the flammable liquid or gel electrolytes found in conventional Lithium-ion batteries (or Li-ion batteries) with a solid electrolyte. This solid component—typically composed of ceramics, sulfides, polymers, or oxides—enables lithium ions to move between the anode and cathode while maintaining structural integrity.
In all-solid-state battery manufacturing, the process eliminates liquid electrolytes, which can address critical limitations of conventional Li-ion batteries, such as safety risks, energy density ceilings, and thermal instability. This pushes the energy industry to evolve. With their potential, all-solid-state batteries can improve the performance of electric vehicles (EVs), consumer electronics, grid-scale storage, and more.
This gives the all-solid-state battery entirely new material architectures and fabrication techniques, unlike conventional Li-ion batteries. In this article, we will explore how all-solid-state battery manufacturing works and diverges from Li-ion batteries.
Structure of Li-ion and All-Solid-State Batteries
At its core, an all-solid-state battery shares the same fundamental purpose as a Li-ion battery: storing and releasing energy through the reversible movement of lithium ions between electrodes.
However, as mentioned above, its architecture is different, which is essential for understanding the all-solid-state battery manufacturing process:
1. Electrodes
Like conventional Li-ion batteries, all-solid-state batteries consist of an anode (negative electrode), and a cathode (positive electrode).
In all-solid-state battery manufacturing, the cathode often employs high-capacity cathodes, such as lithium nickel manganese cobalt oxide (NMC). It is similar to those in Li-ion batteries.
However, the materials and design of the anode differ:
- Conventional Li-ion batteries often use graphite anodes, which intercalate lithium ions during charging.
- All-solid-state batteries typically utilize lithium metal, a material long avoided in liquid systems due to dendrite formation (needle-like growths that can cause short circuits).
2. Electrolyte
The electrolyte is used in all-solid-state battery and conventional Li-ion battery manufacturing. They are all used for conducting ions, but ASSBs starkly contrast with the liquid electrolytes used in conventional Li-ion batteries. Here’s a breakdown of the key differences:
Aspect | Li-ion Battery | All-Solid-State Battery |
Material | LiPF₆ in organic solvents | Ceramics, Sulfides, Polymers, Oxides |
Role | Allows electrode immersion | Blocks electrons; physically separates electrodes |
Safety | Flammable solvents pose fire/explosion risks | Non-flammable–no leakage and thermal runaway |
Manufacturing Technique | Simple electrolyte filling (wet process) | High-temperature sintering or precision thin-film deposition |
3. Interface
In Li-ion batteries, liquid electrolytes easily permeate porous electrodes, ensuring intimate contact. For solid-state battery technology, the interfaces between the electrolyte and electrodes are potential bottlenecks. Poor interfacial contact increases ionic resistance, degrading performance. The following factors must be considered:
Chemical Compatibility: Reactions between the electrolyte and electrodes can form resistive layers (e.g., Li₂CO₃ on lithium metal).
Mechanical Stress: Repeated expansion/contraction of electrodes during cycling can fracture brittle electrolytes.
Processes of Li-ion and All-Solid-State Battery Manufacturing
It is important to understand their difference in the manufacturing process. It helps fully grasp the safety, cost, and scalability of conventional Li-ion and ASSB manufacturing:
Aspect |
Li-ion Battery Manufacturing | All-Solid-State Battery Manufacturing |
Electrolyte Integration |
Liquid injected post-assembly |
Solid layers pre-integrated during stacking |
Key Equipment |
Slurry mixers, coating machines, filling systems |
Sintering furnaces, ALD tools, dry-room robotics |
Cycle Time |
Minutes for electrolyte filling |
Hours for layer sintering/pressing |
Material Sensitivity | Moderate (moisture-sensitive anodes) |
Extreme (sulfides degrade at ppm-level humidity) |
Safety of Li-ion and All-Solid-State Battery Manufacturing
As mentioned above, these manufacturing differences directly impact the safety profiles of both technologies.
One of the most significant safety aspects is non-inflammability. By replacing liquid electrolytes with solids, ASSBs eliminate the risk of combustibility, helping prevent fire and more serious explosions in manufacturing.
Additionally, several other factors further emphasize the safety advantages of all-solid-state battery manufacturing:
Safety Aspect | Li-ion Battery Manufacturing | All-Solid-State Batteries Manufacturing |
Thermal Risks | High risk of thermal runaway during formation cycling | Non-flammable electrolytes resist ignition |
Electrolyte Handling | Hazardous liquid filling | No solvent-dry processing of solid electrolytes |
Dendrite Suppression | Additives/separators; prone to defects | Solid electrolytes physically block dendrite growth |
Gas Generation | Gassing during formation requires venting systems | Minimal gas evolution (no liquid decomposition) |
Cost and Scalability of Li-ion and All-Solid-State Battery Manufacturing
While all-solid-state batteries offer excellent safety performance, their current manufacturing costs far exceed those of Li-ion systems. Estimates suggest that solid-state batteries are currently more expensive to produce. For instance, some projections indicate that solid-state battery prices could fall between $80 and $90 per kWh by 2030, while conventional Li-ion batteries could reach $60 per kWh within the same timeframe.
This disparity can hinder the large-scale production of all-solid-state batteries. Here are additional key points:
- Manufacturing Complexity
The manufacturing of all-solid-state batteries involves intricate production processes, including the precise fabrication of solid electrolytes and the management of interfaces between solid components. This complexity makes scaling up production more challenging than the well-established processes for Li-ion batteries.
- Infrastructure Limitations
Existing battery assembly lines are primarily designed for Li-ion battery production. Adapting these facilities to meet the unique requirements of ASSBs requires significant investment and time.
Advanced All-Solid-State Battery Manufacturing by Lead
At Lead, we have an independent R&D team to bridge the gap between Li-ion batteries and ASSB. Our all-solid-state battery manufacturing solution tackles scalability head-on, combining cutting-edge technology with process optimization to overcome traditional bottlenecks. Here’s how it works:
1. Adopting the Dry Electrode Process
• Dry coating minimizes the waste of expensive solid electrolytes (e.g., sulfides) by 15–20% compared to slurry-based methods. It can also reduce overall capital investment by around 30% by eliminating solvent recovery systems and drying ovens.
2. Operating with Superior Coating Efficiency
• In the anode, the coating speed of Lead’s all-solid-state battery manufacturing solution exceeds 80 m/min with thickness uniformity controlled to ±2 μm.
• In the cathode, the coating speed can surpass 50 m/min, maintaining precision for composite electrodes (active material + solid electrolyte).
3. Reducing Process Complexity
• From raw material handling (e.g., air-sensitive sulfides, lithium metal) to finished cell assembly, Lead’s fully automated lines reduce manual intervention by 20%.
• Robotic systems manage brittle ceramic electrolytes and lithium metal foils with micron-level precision, minimizing breakage.
4. Manufacturing Safely and Stably
• Lead’s all-solid-state battery manufacturing solution is engineered for specific materials, including moisture-sensitive sulfides (<1 ppm H₂O environments) and reactive lithium metal (argon-atmosphere handling).
• In-line quality control systems, such as proprietary specialized testing and analysis software, ensure the perfection of the battery production.
Conclusion
All-solid-state batteries (ASSBs) represent a transformative leap in energy storage. Compared to conventional lithium-ion systems, they offer unparalleled safety, higher energy density, and sustainability. Yet, their potential hinges on overcoming manufacturing complexity and scalability challenges.
Our Lead turnkey solution redefines all-solid-state battery production through innovations such as dry electrode processing, end-to-end automation, and robust safety protocols. With it, we believe we can bridge the gap between lab breakthroughs and mass adoption of all-solid-state batteries to push the industry forward and make people’s lives safer and greener.
Please visit our Lead’s official website to get more insights on battery manufacturing!
References
- Available at: http://en.wikipedia.org/wiki/Solid-state_battery
- Available at: http://bpb-us-e1.wpmucdn.com/blog.umd.edu/dist/7/477/files/2021/04/296.pdf
- Available at: http://onlinelibrary.wiley.com/doi/full/10.1002/eem2.12613
- Available at: http://www.qa-group.com/en/glossary/dendrites/
- Available at: http://pubmed.ncbi.nlm.nih.gov/30680811/
- Available at: http://revolutionized.com/solid-state-vs-lithium-ion/
- Available at: http://www.ufinebattery.com/blog/solid-state-battery-vs-lithium-ion-a-comparative-analysis/
- Available at: http://futurebatterylab.com/costs-of-solid-state-batteries-expensive-premium-solution-or-affordable-all-rounder/